
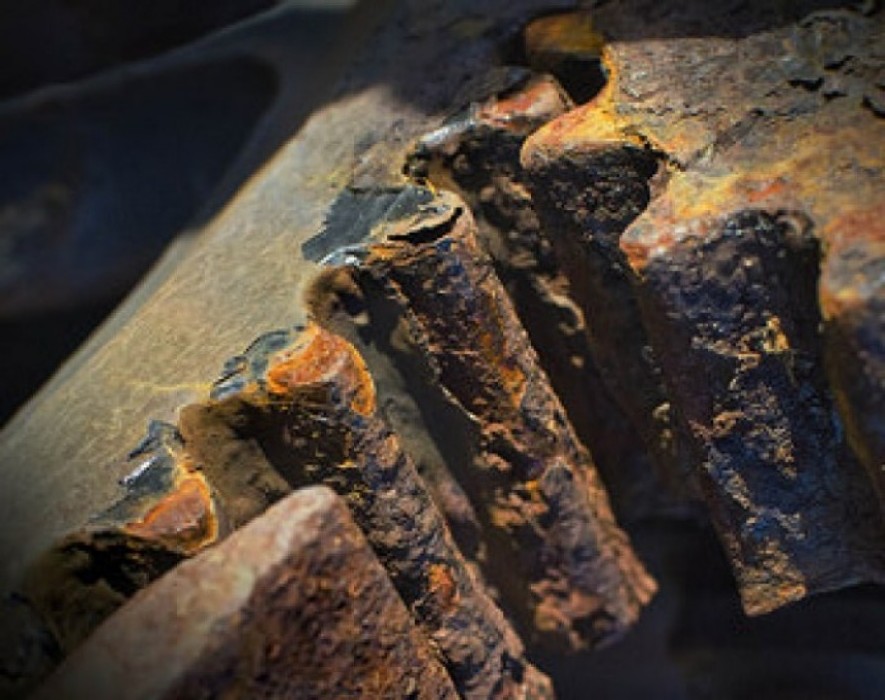
Even though regular paints are advertised as corrosion-resistant, their protection is limited, especially in immersive environments. Ordinary paints create an impenetrable barrier between the metal and environmental stressors. What are The Benefits of Zinc Oxide Primer Paints? Other electrically active metals include magnesium and aluminum, which can apply as a coating on other metals for their galvanizing properties. Hence, it can act as the sacrificial anode when corrosion occurs. Zinc is more electrically active compared to other structural materials like steel. Therefore, when zinc comes into contact with steel, it provides cathodic protection and galvanizing properties. The “sacrificial” term refers to the zinc coating corroding itself while protecting the integral component or structure. The high zinc concentration in the primer means it possesses sacrificial anodic properties. The presence of zinc makes these primers different from regular paint primers. How Does Zinc Oxide Work in Primer Paint?Ī zinc primer is a chemical substance that consists of large amounts of silver-white metal zinc. Hence, to improve the durability of iron or steel, a zinc-rich primer is used as a preparatory coating to protect it from corrosion. Sometimes, a metal-like steel may rust if placed under too much physical pressure, causing it to break down ultimately.Īs metal applies as a building material in various large projects, the surface must withstand environmental pressures throughout its lifetime. Corrosion may also occur in metallic surfaces due to electrical current, dirt, and bacteria. We can help find you the best die casting manufacturer for your project requirements.Metal tends to corrode whenever it reacts to oxygen and hydrogen in the atmosphere. Get the Corrosion-Resistant Die Cast Components You NeedĬall us at 40 or contact us to discuss your corrosion resistant die casting project. Should be coated or sprayed for corrosion resistances.Ideal for thin-walled components/tight tolerances.Good corrosion resistance when not subjected to marine or atmospheric salt content.
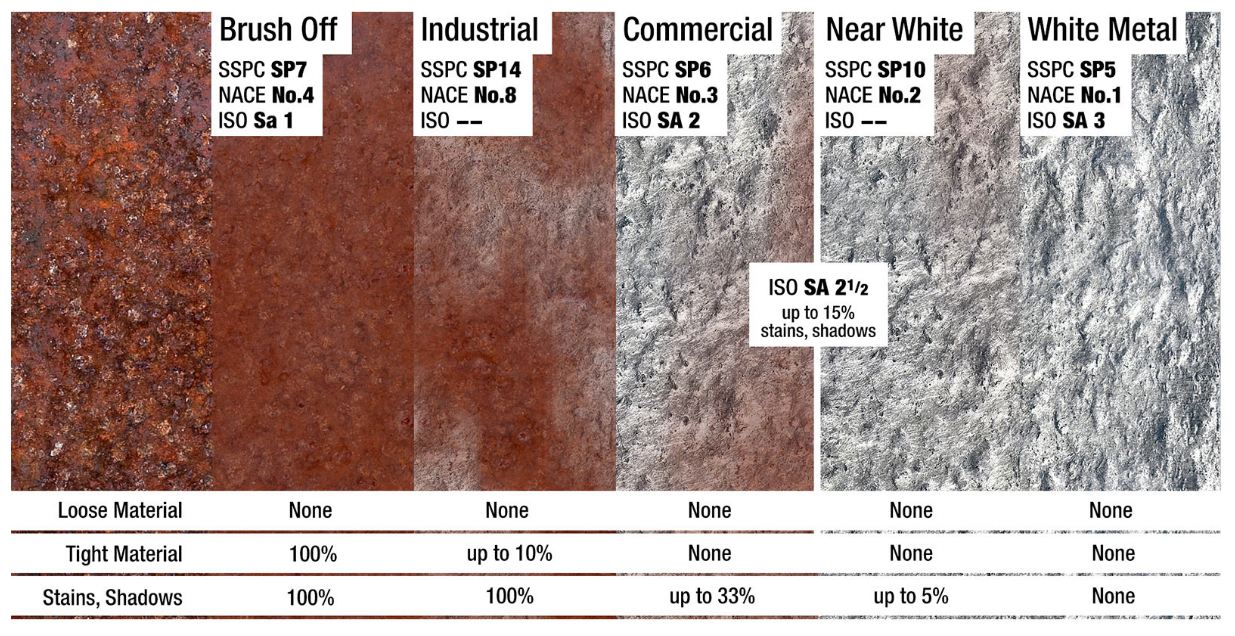
However, the best alloy for your die casting project depends on other factors for consideration. Choosing the Best Alloy for Your Die Cast ProjectĪluminum, zinc, and magnesium all offer different levels of corrosion resistance. Sprays or coatings for magnesium die cast components can provide the galvanic corrosion protection needed for most components. While magnesium provides benefits including lightweight composition and recyclability, it is not inherently corrosion-resistant like aluminum or zinc. While zinc can corrode in harsh atmospheric environments, it is well suited for most die cast components including automotive die cast parts. Marine and atmospheric environments with salt will eventually corrode zinc die cast components. Due to its smooth surface finish, zinc works best for applications that will not be subjected to high temperatures. Ideal for automotive or electoral applications, zinc alloys provide excellent corrosion-resistance. While aluminum does not rust, it can corrode depending on environmental factors. With little to no iron in its chemical composition, aluminum is a rust-proof alloy. Aluminum can also withstand high heat temperatures making it a versatile choice for different die casting methods.
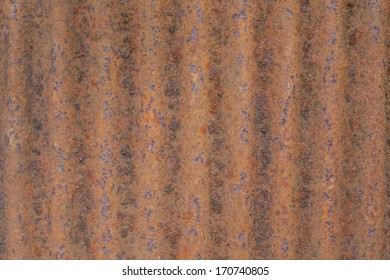
Aluminum’s mechanical properties of lightweight with high strength-to-weight ratio make it an ideal choice for a wide range of components and parts. Aluminum Die CastingĪs a well-known metal for its corrosion-resistance, aluminum is a popular die cast metal option. Less common die cast metal includes brass, copper, or other specialty alloy materials. While each metal type offers corrosion resistance, the levels of rust protection vary. The best die casting methods and metals will be largely determined by your component’s complexity and functionality.Īluminum, zinc, and magnesium are common metal materials used for die cast metal parts. With die casting being an efficient way to manufacture complex components, it is important to understand the benefits of commonly used metals for die cast parts.
